JOURNAL
Damascus Steel Eyewear: Metal with warmth and character
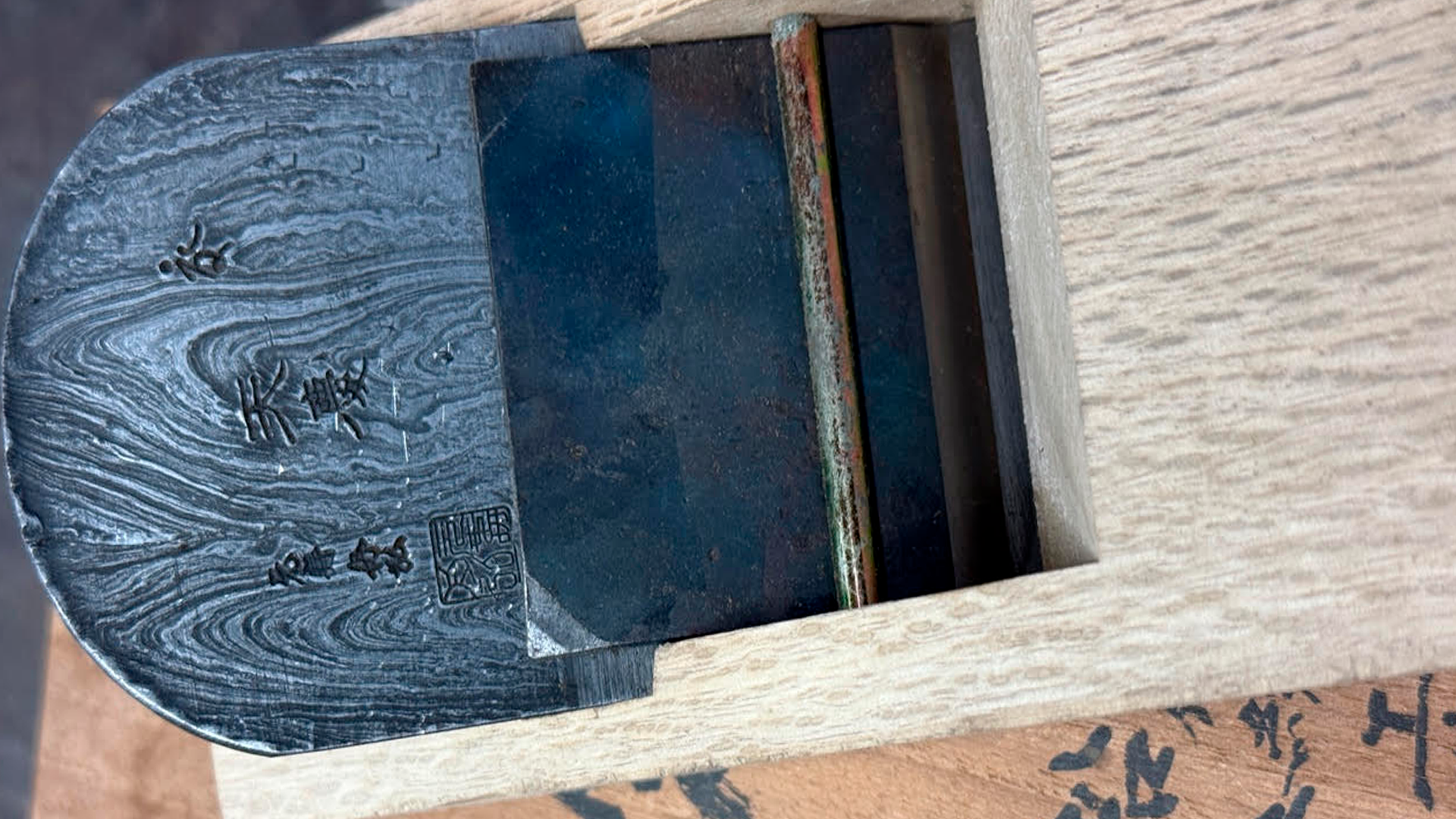
Kajimachi - hundreds of years of blacksmithing history
We are located in Sanjo city in Niigata. In records going back to the 1600’s Sanjo as been known as a “kajimachi” or blacksmithing town. What started out as forged nails and other goods to support the growing Edo (now Tokyo) across the mountains was followed by agricultural tools, woodworking tools, and kitchen knives. Today Sanjo is known as one of the great blacksmithing cities of Japan, home of some of the finest knife and tool makers in the world.
The road to Damascus steel eyewear - where it all began
In Sanjo, there is a “Blacksmith Dojo”, a place where the general public can try their hand at blacksmithing and knife sharpening. I took our whole team to go make a hand forged Damascus steel letter opener.
I am a tool buff (woodworker…) and have hand forged chisels and planes made by some of the finest blacksmiths in the Japan, and have long been mesmerized by the natural undulating patterns of “Mokugane” (the Japanese characters literally translate as “wood metal”) or Damascus steel. Mokugane is a fitting word not only in that there is a “grain” in the steel, but as there is a “warmth” that isn’t found in other metals.
I still have and use the Damascus steel letter opener, it is beautiful. Then the idea of making eyewear from the Damascus steel hit me (OK, there may have been a couple of whiskey’s involved…), something truly “Made in Sanjo”. I do a bit of blacksmithing – hand forged a temple or two, honestly, not terribly practical for making eyewear – yes, making one is doable, making two exactly the same is very hard, and more than that exhausting. There are only a couple of steel makers in Japan that can make Damascus steel, so we started working together to design material for eyewear.
The president of the company is a metallurgist and I am a chemical engineer…we hit it off instantly. The first pair of glasses I made was from stainless steel used to make knives…absolutely the most uncomfortable pair of glasses I ever made…high hardenable steel content made it impossible to adjust (it was beautiful though). So I worked with the manufacturer for a stainless steel combination that would be robust, finish beautifully, and be adjustable.
What we ended up with is 15 layers consisting of 2 types of stainless steel, each layer starts out 1cm thick and is hot forged and hot rolled over and over until the total package is less than 1.8mm (yes, each layer is around 0.1mm). We then do further work to thickness and finish the metal ending up at 1.6mm.
How we turn raw mokugane into eyewear
When it is raw, it is not much to look at, a dull matte flat cold gray, but then the magic happens. Damascus steel is incredibly difficult to machine, it eats tools. Hard and soft layers melding together dull and break end mills and drills (especially the size used for eyewear), it took a lot of work to be able to accurately manufacture the parts but we have dialed in the process.
We use machines and chemistry to cut, bend, form and shape the material and in doing so the various layers are brought to light. The parts are then polished in a barrel and sand blasted, and maybe finished by either blackening the steel or maybe an antique gold plating process. Now you can see and feel the warmth.
We continue developing new materials, now we have an even thinner version to play with, look forward to showing that to you soon!!!
Categories
Latest posts